“小”改进带来“大”效益
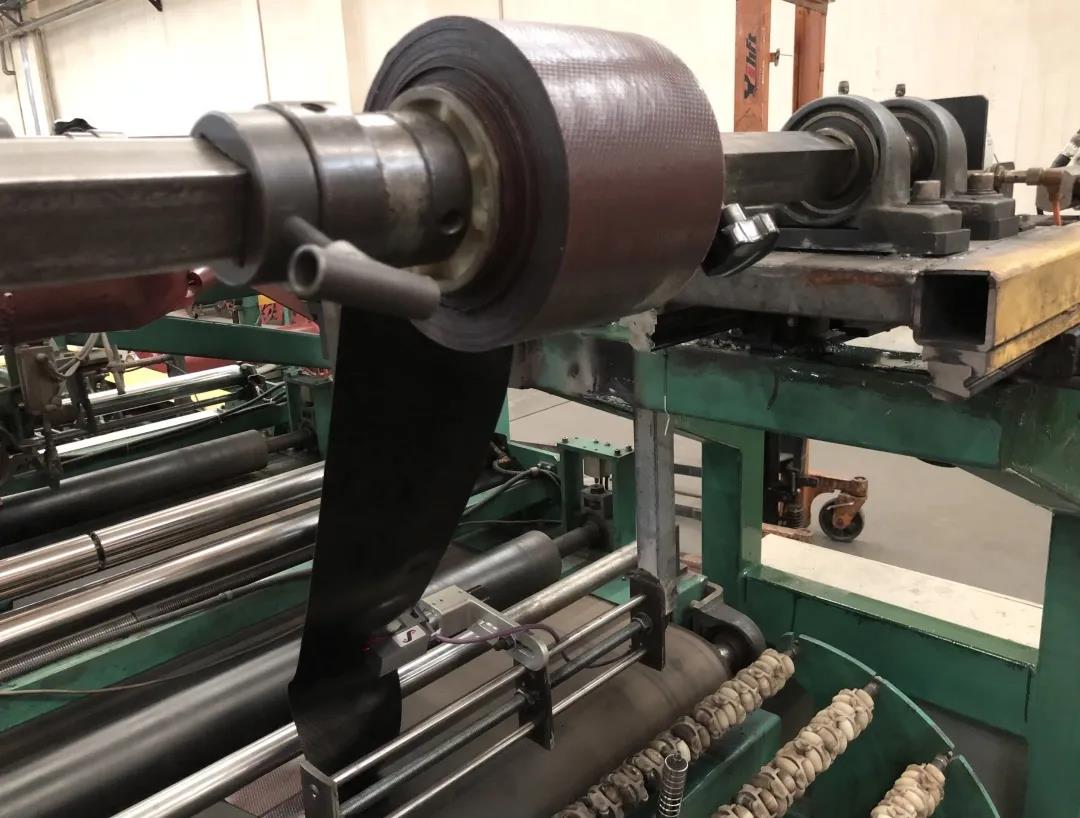
“贴合方式的改进,提高了工效,降低了劳动强度,现在工作起来省时省力多了。”部件车间员工指着眼前这个新式装备赞不绝口,大家也都纷纷伸出大拇指称赞。
到底是个什么“利器”得到大家的认可和称赞呢?
枣矿橡胶公司八亿橡胶部件车间A1 1#压出设备由于早时制造商受设计理念所限,压出胎侧胶片无法热贴合、无法压合排气线,故长期使用冷胶片贴合的方式生产。此贴合方式胶片粘性差,不利于部件粘合,有造成成品脱层的隐患。贴合过程中常出现垫布打褶问题,冷却水会从垫布打褶处浸入,影响胶片粘性,并需要经薄胶片与多刀纵裁两个步序,增加了操作岗位,降低了工效。
经过现场多次调研,该车间提出胶片贴合方案改进的课题,在反复论证、实践后,胎侧胶片由原冷贴升级为热贴。在课题小组的努力下,他们优化装置结构,确保符合胎侧垫布贴合要求,调整口型板于胶片定位点添加定位辅助线,提升胶片贴合精度,调整两辊压延机上方千页片压合力度,使其可同时匹配胎面、胎侧胶片贴合生产。
通过设备技改,提升胎侧胶片粘性、降低成品胎侧泡问题的同时,减少了薄胶片大卷制作、胶片多刀纵裁两个生产工序,提高了生产工效。并为部件定线生产提供了可行性,避免了一线员工频繁更换胶料而带来的劳动强度增加。
在八亿橡胶成型车间,直裁工序生产过程中之前频繁出现胶片定位偏歪等问题,造成垫胶移位、胎冠脱层,影响产品合格率。经车间现场查看分析,发现原装设备无纠偏定位装置,每次换料都需人工移动胶片进行定位,但在生产过程中也会出现跑偏现象,影响贴合质量。针对这一难题,成型车间召集相关人员专题研究,决定对胶片贴合定位装置进行升级改造。项目人员主动出击、集合力量,出方案、画图纸、报计划,经过半个月时间,完成了两条直裁线定位装置改造。改造后胶片定位精准,机台人员反映使用效果良好,并节省了外委资金。
“现在不需要我们人工移动胶片进行定位了,劳动量比原来明显降低,而且现在的定位装置很少出现胶片定位偏移等问题,产量和合格率明显提升。”该车间员工徐妍说。